齐博阳,陈冬,王文举
(南京理工大学能源与动力工程学院,南京210094)
摘要:气化技术作为固体燃料(如煤和生物质等)清洁利用的重要方式,越来越广泛地被应用于生产合成气的工程实践中。针对煤与生物质在单独气化时存在转换效率低、气体产物热值低以及焦油含量高等问题,提出了共气化技术以改善气化工艺。文中主要介绍了基于计算流体力学(CFD)的煤与生物质共气化仿真模拟的研究,论述了两种固体燃料在单独气化和共气化时的反应机理,并详细介绍了冷态和热态流化床共气化CFD模拟所用到的模型。
目前全球绝大多数能源均由传统化石燃料所提供。随着能源需求量的不断增加,燃料资源总量也在日益减少,同时在煤等燃料的燃烧利用过程中会产生大量的NOx、SO2以及颗粒物等污染物,会对环境造成严重的影响[1]。所以,对资源进行更加清洁高效的利用是目前亟待研究和解决的问题。
在现有的能源利用技术中,气化则被视为传统能源清洁高效利用的重要方式之一[2],其中对煤与生物质的气化研究较为广泛,此外由于拥有较为适中的温度、物料粒径等条件,使得流化床气化成为活性较高的煤种与生物质等燃料气化的主要方式。固体燃料流化床气化示意图及气化特点如图1所示。
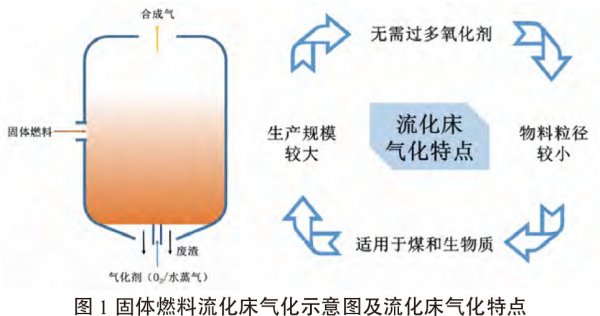
在已发展较成熟的燃料单独气化技术的基础上,研究人员提出了煤与生物质的共气化技术[3]。煤与生物质在共气化过程中产生了协同作用,弥补了两种燃料单独进行气化过程中的不足,打破了气化原料选择的限制,同时还可以提高气化时碳的反应速率,抑制焦油的生成并减少污染物的排放[4]。所以共气化技术在将固体燃料转化为合成气的同时,提高了能源的利用率,并且减少了一部分化石能源的消耗。由于生物质和煤的气化需要在900~1000℃的高温条件下进行,对实验设备有较高的要求。此外,在对气化过程进行实验探究时,耗时较长,危险性也较高。而通过计算流体力学(CFD)等数值模拟的方法则可以使得研究工作的成本较低,能节省更多的时间、人力和物力。
CFD在流化床中的应用主要有三个方面[5],分别是流化床结构设计与操作条件的优化;模拟流化床冷态气固两相流,研究其中颗粒流动的规律;模拟流化床中热态的化学耦合,建立热态化学反应模型。李乾军[6]等人利用ANSYS Fluent软件分析了压力对喷动流化床流动特性的影响,发现当喷动风占总风的一半时有助于煤气化的进行,并且模拟与实验结果的吻合度较好。邓中乙[7]等人建立了非稳态三维喷动床煤气化动力学模型,包含了气固两相流、挥发分析出、焦炭气化反应以及气相均相反应等子模型,通过与实验结果对比发现入口中心的床温最高,而且生成气体的质量在加压后有了明显的提高。GerberS[8]等人建立了二维鼓泡流化床模型,通过模拟木屑的气化过程发现CO和CO2对热边界条件很敏感,同时焦油的产生受气化时操作条件的影响较大。
1煤与生物质的气化过程原理及研究
固体燃料气化过程如图2所示。煤和生物质等固体燃料气化过程通常包括预热、热解和气化三个部分,预热阶段主要脱除了水分,而最终产生的合成气则是由热解产物通过气相反应和气固反应得到的。
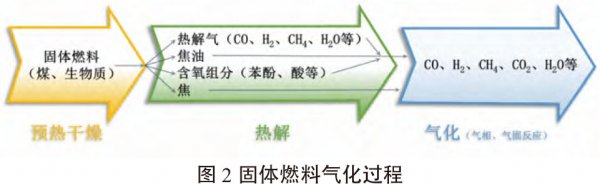
1.1煤气化
煤可以根据挥发分的含量不同分为无烟煤、烟煤和褐煤这几大类,对于不同种类的煤气化过程均可分为三个阶段[9],首先是室温~300℃的干燥阶段,此时煤的外形基本不发生变化;然后是300~610℃的热解阶段,此阶段会生成大量煤气和焦油等挥发分;最后是610~970℃的焦炭气化阶段,主要为脱挥发分后的焦炭与CO2的反应阶段,即Boudouard反应,反应可用式(1)来表示:
C+CO2→2CO-172kJ/mol(1)
影响煤热解气化的主要因素包括煤化程度、粒径和孔结构分布等原料煤性质,以及升温速率、压力和停留时间等外界条件[10]。
刘臻[11]等人利用湍流气相反应模型,计算了煤气化过程炉中的温度场、浓度场以及碳转化率分布,发现湍流气相反应模型对于火焰区温度场和浓度场中的计算影响较大,但是对气化炉后部的影响较小。秦丽娜[12]等人基于DAEM分布活化能模型建立了热解反应动力学模型,发现将终温控制在550℃,升温速率设为10℃/min有利于挥发分的完全析出。
1.2生物质气化
生物质主要由纤维素、半纤维素和木质素以及少量灰分组成,其气化过程同样包括三个阶段[13],首先是预热解阶段,在120~200℃时H2O、CO2和CO释放导致原料重量轻微减少;然后是固体热解阶段,主要发生在300~600℃;最后是焦炭气化阶段,此阶段与煤焦气化类似,属于典型的气固反应过程。生物质的气化过程主要受脱挥发分后生成焦的气化反应性影响,故气化过程主要影响因素包括气化温度、升温速率以及气化剂的种类等。
在生物质气化的数值模拟方面,李乾军[14]等人利用基于欧拉多相流的动力学模型并自编了化学反应子模型,从而建立流化床气化动力学模型对生物质气化过程进行了模拟,结果与实验基本吻合,同时发现随着生物质粒径的减小,所生成的CO、H2的体积分数以及蒸汽分解率都相应增大。张鹏威[15]等人通过Fluent软件模拟了生物质-水蒸气气化反应,发现随着温度的升高碳转化率和气体总产率均增大,CO和H2的生成受床层高度影响较大,同时模拟结果可以说明水蒸气作为气化介质可以增加H2的产量。
1.3煤与生物质共气化
由于传统化石燃料的大量消耗以及利用时产生环境污染,生物质等可再生能源的利用越来越受到重视,但是生物质资源的供给受季节的制约,同时其较低的能量密度以及气化时生成较多的焦油,这些因素都使得生物质的利用效率较低[16]。因此,基于已有的单独气化技术,研究人员提出了煤与生物质共气化,利用两种不同燃料间的协同作用来提高能源的利用效率并弥补燃料单独气化时的缺陷。
研究人员在共气化研究中发现,从生物质转移到煤中的H自由基和OH活性基团,以及生物质中如钾(K)等碱金属的催化作用促进了煤的气化过程,并且提高了合成气的产量,即生物质与煤之间产生了协同作用[17]。碱金属的催化机理如式(2)~(4)所示[18]:
M2CO3(s,l)+2C(s)←→2M(g)+3CO(g)(2)
2M(g)+CO2(g)←→M2O(s,l)+CO(g)(3)
M2O(s,l)+CO2(g)←→M2CO3(s,l)(4)
当碱金属为钾时,气化反应中碳表面K+的氧化还原催化反应机理如图3所示[19]。
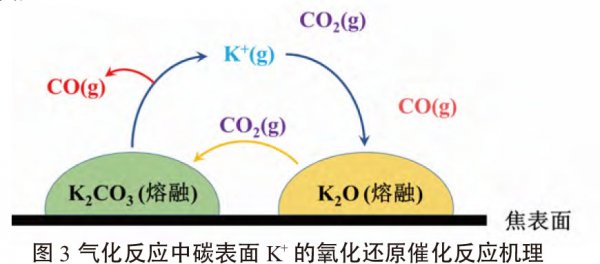
PanYG等人[20]发现在生物质与煤进行共气化时,随着生物质掺混比例的增加,煤中的碳转化率以及所生成合成气的热值均在增加。Lu等人在研究中发现,煤在与生物质共热解时挥发分释放的初始和终了温度取决于生物质的掺混比例以及煤阶。Wang等人[21]发现,当掺混比低于50%时生物质会促进煤的热解,而当掺混比高于50%时煤与生物质之间的协同作用将会消失。由以上研究可以看出,由于煤和生物质间性质差异较大,故共气化过程中的影响因素较单独气化时更多,如气化温度、原料掺混比例、气化剂种类、生物质种类以及掺混方式都会影响共气化反应。
在CFD模拟仿真方面,张锐[5]搭建了流化床中的气化反应动力学模型,通过数值模拟发现,当共气化中褐煤掺混比增大时,炉膛温度升高且温度最大值向着炉膛上方移动,同时合成气中CO、H2和CH4的浓度下降,而CO2的浓度上升。Armstrong等人将鼓泡流化床中煤和生物质共气化反应视为非均相反应,并采用脱挥发分模型对煤和生物质的共气化以及两种燃料对应的焦之间的共气化过程进行了模拟,最后将模拟结果与文献中报道的实验值进行了比较。何志超[30]利用CFD对木屑与褐煤的共气化进行了数值模拟,发现当空气当量比(ER)由0.22上升到0.38时,合成气中CO、H2和CH4的体积分数减小,但气体产率和碳转化率增大,气化效率则在空气当量比为0.26时达到最大值。Chen[22]等人同样通过对煤和生物质的共气化进行CFD模拟,发现碳的氧化反应在提高反应温度的同时,也会使燃料颗粒的脉动速度增加,此外生物质颗粒的波动能大于煤颗粒的波动能。
2流化床冷态数值模拟
流化床内物料的流化状态依赖于气固两相流的流动,对两相流动特性进行研究,可以得到流化床内的压力分布、颗粒浓度及速度的分布情况,从而确定床内物料的流化状况。此外,两相流动对气化时的气固反应影响大,它会影响流化床内热量、动量和质量的传递,以及气化时反应速率的快慢[23],所以,对流化床内气固两相流的模拟研究是流化床气化模拟的重要部分[24]。在应用CFD对气固两相流进行模拟时,模型的精确程度直接影响到数值实验的成功与否,其中模拟方法主要分为两大类,分别是双流体模型(Two Fluid Model,TFM)和离散颗粒模型(Discrete Particle Model,DPM),此外还有在上述两种模型的基础上发展出来的小室模型和能量最小多尺度模型等。下面主要介绍双流体模型和离散颗粒模型。
2.1双流体模型
双流体模型是由Gidaspow[25]等人于1986年提出的,在双流体模型中,颗粒相被处理为类似流体的连续相,即颗粒相被视为与真实流体互相渗透的拟流体,两相流场则视为两种不同流体间相互作用和各自运动的整体作用效果[50]。双流体模型中主要包括了连续流体模型、传统双流体模型和基于颗粒动力学理论的欧拉双流体模型。
Benyahia[26]等人利用双流体模型对循环流化床上升段中的气固两相流进行了模拟,模拟中炉膛在径向的颗粒浓度和流量与实验结果相符,同时还发现当流化床底部的密相区中固体空隙率减少时,炉膛内固体颗粒温度与粘度呈指数上升。Luben[27]等人在双流体模型的基础上分别考虑了固相粘性和不同气固耦合修正模型,通过模拟得出了不同结果,因此他们认为有必要建立一个更加完善的修正模型。Goldschmidt[28]等人采用了双组分颗粒气固两相流模型,模拟了鼓泡流化床中双组分颗粒的流动特性,发现在考虑了颗粒团间碰撞的能量消耗后模型能够更加贴近流化床中真实的流动情况。在双流体模型中,因为将颗粒视为连续介质,所以无法从颗粒尺度上对问题进行解析,所以更适合对宏观流动进行模拟,同时由于双流体模型考虑因素较全面且计算量较小,所以更多地被用于实际工程的模拟中。
2.2离散颗粒模型
离散颗粒模型又称为颗粒轨道模型,不同于根据欧拉坐标系建立的双流体模型,离散颗粒模型是基于拉格朗日坐标系建立的[29]。此模型中的固体颗粒被视为离散相,通过在拉格朗日坐标系中建立单颗粒的运动方程,进而对大量的颗粒轨迹进行统计分析,最后获得颗粒群的运动情况即颗粒相流场[30]。
Tanaka[31]等人利用离散颗粒硬球模型模拟了垂直管道中的气固两相流动,发现不管炉膛中的颗粒浓度大或小,颗粒间的碰撞都会严重影响着颗粒的扩散运动。Hoomans[32]等人同样采用离散颗粒硬球模型对二维流化床中的气固两相流动进行了模拟,研究发现颗粒间的碰撞会严重影响炉膛内生成气泡的形状。Tsuji[33]等人在1993年提出了适用于二维气固流化床的离散颗粒软球模型,成功模拟了流化床内颗粒循环运动和混合的过程,显著提高了离散颗粒模型模拟的计算能力。由离散颗粒模型的模拟机理可知,该模型可以对颗粒间的相互碰撞进行模拟分析,所以与双流体模型相比,其更适合从颗粒尺度对气固两相流的机理进行探究,但由于需要对大量颗粒轨道进行统计分析,离散颗粒模型的计算量非常大,故其对颗粒的研究规模受到计算机CPU、内存等运算硬件设备的限制,不适宜应用于工程实际中。
3流化床气化热态模拟
在冷态模拟的基础上,气化热态模拟中加入了能量等控制方程和化学反应,并选取P1辐射模型,最终将流动、传热和化学反应模型进行耦合,从而对共气化过程进行数值模拟。
3.1模型控制方程
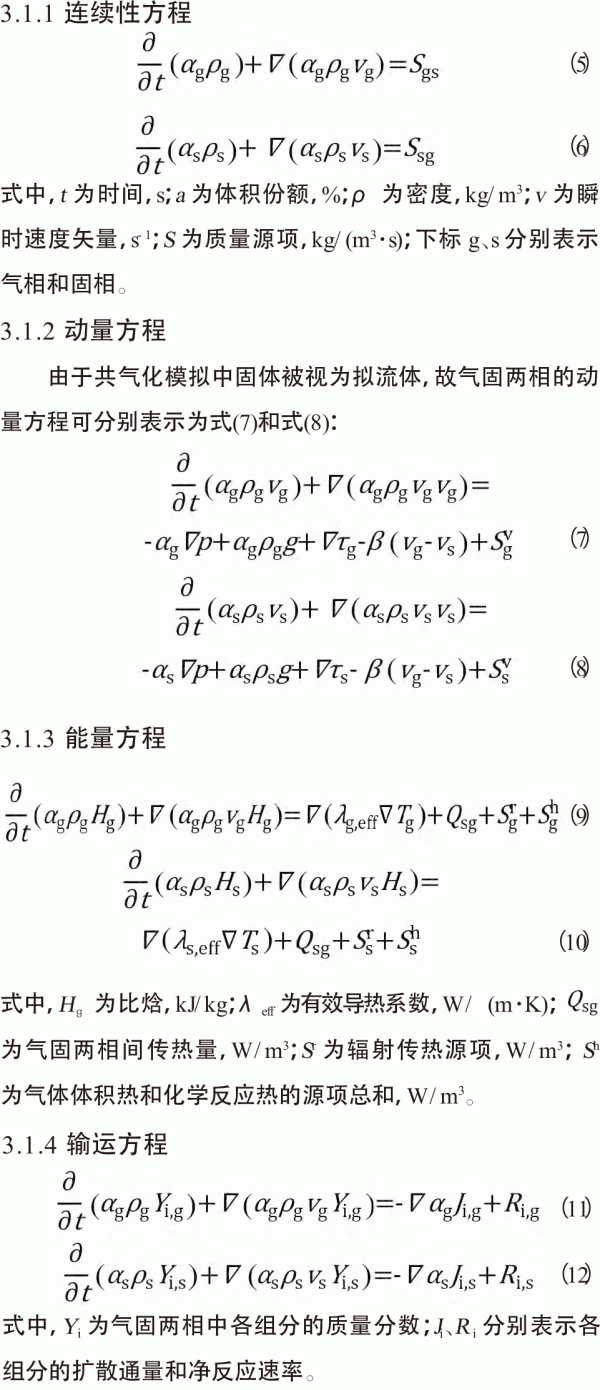
3.2化学反应模型
共气化过程中包含了众多复杂的物理和化学过程,为简化模型便于进行数值模拟,计算中主要考虑挥发分析出、气相均相反应以及气固异相反应这三个反应模型。
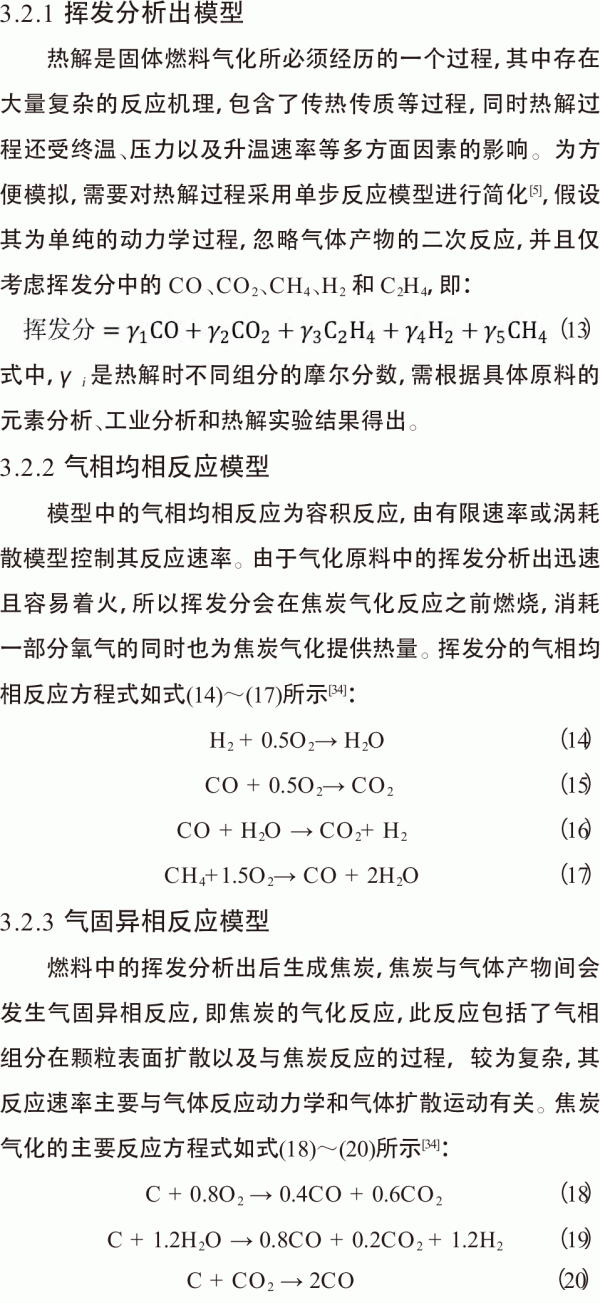
3.3湍流-气相反应耦合模型
在燃料气化的数值模拟过程中,湍流-气相反应耦合模型反映了湍流和气相反应间的相互作用及影响,同时决定了模拟的收敛性和最终结果的准确性,是气化模拟中极为重要的一部分。目前气化炉中常用的湍流-化学反应耦合模型主要有概率密度函数模型(probability density function,PDF)、涡破裂模型(eddybreakup,EBU)和涡耗散模型(eddydissipation model,EDM),这三类耦合模型在气化方面的研究概况见表1。
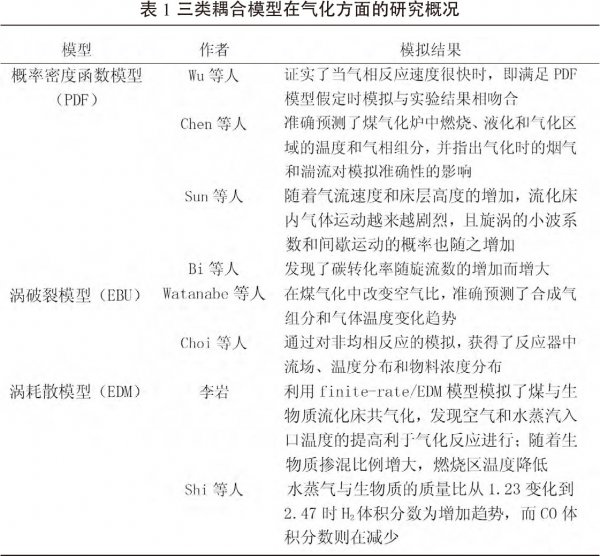
3.3.1概率密度函数模型
概率密度函数(PDF)是一种基于平衡反应和快反应两种反应假定的模型,可以假定反应速度足够快,从而使得任一时刻中的气相均位于化学平衡状态[11]。Wu[35]等人通过实验和模拟同样验证了当床内温度和压力较高时,由于气相反应速度快使得产生的合成气在出口时已接近平衡状态,所以模拟结果和实验结果吻合度较高。Chen[36]等人利用PDF模型对煤气化过程进行了模拟,模型对气化炉中燃烧、液化和气化区域的气相组分及温度预测较为准确,同时也表明了烟气和湍流对模拟结果的准确性有很大的影响。Sun[37]等人发现随着气流速度和床层高度的增加,流化床内气体运动越来越剧烈,不同气体流速下产气体积分数的分布如图4所示,此外旋涡的小波系数和间歇运动的概率也随之增加。Bi[38]等人也利用PDF模型模拟了气化炉中的湍流-气相反应,通过比较模拟与实验结果验证了模型的可靠性,并且发现碳转化率随着旋流数的增加而增大。PDF模型与一般的湍流模型相比,可以更加完整、准确地模拟湍流流场,尤其是对于符合其反应假定的射流以及高温高压下湍流-反应的模拟,模拟结果均与实验值有较高的吻合度。
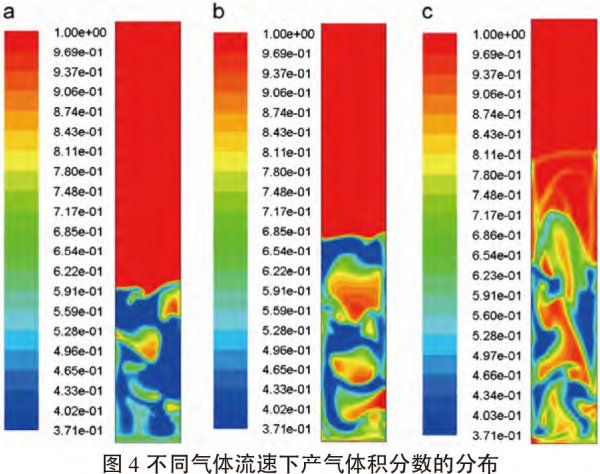
3.3.2涡破裂模型
涡破裂模型(EBU)由Magnussen[39]等人提出,该模型将燃烧速率与旋涡耗散率相结合,用反应物的平均浓度、湍流动能和耗散率来表示反应速率,并且不要求对反应物的波动进行预测。Watanabe[40]等人利用EBU模型对煤气化进行了模拟,验证了模型的有效性,并且在改变空气比的条件下,精确预测了气体温度的变化趋势以及合成气的组分,日本黑煤气化过程模拟值与实验值对比结果如图5所示,在对日本黑煤的气化过程进行模拟时,发现模型对CO和CO2体积分数的模拟与实验结果吻合度较高,而H2体积分数高于实验值,H2O的体积分数则低于实验值。Choi[41]等人使用EBU模型模拟了气化中的非均相反应,得到了气化炉内的流场、温度以及物料浓度分布等详细结果,同样验证了EBU模型的可靠性。在EBU模型中,反应平均速度只与低温反应物和高温燃烧产物间的湍流混合作用有关,模型可以对反应器中的温度场、流场以及产物的组分等进行较为准确的模拟。
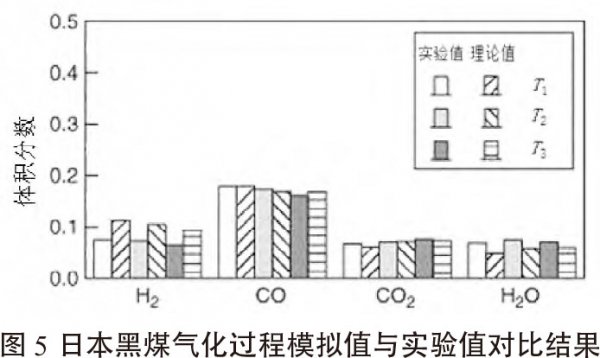
3.3.3涡耗散模型
在涡耗散模型(EDM)中,湍流气相反应被视作湍流脉动与化学反应之间相互作用的结果[11],反应速率受湍流控制,故任一反应均拥有相同的湍流速率,因此EDM模型只适用于总包反应。在对其进行修正后,有限速率/涡耗散模型(fi-nite-rate/EDM)得到了较另两类模型更为广泛的应用,它利用湍流脉动和Arrhenius公式来控制反应速率,使得模型可用于计算多步反应[42]。Shi[43]等人采用finite-rate/EDM模型模拟了生物质在流化床中的气化过程,如图6所示为水蒸气与生物质的质量比为1.53时各类气体体积分数的分布,模拟中H2的体积分数先增加后保持不变,而CO则先减少后维持稳定,且质量比从1.23变化到2.47时H2体积分数为增加趋势,相反地CO在减少。李岩[42]同样利用finite-rate/EDM模型对流化床中的煤与生物质共气化过程进行了模拟,发现提高燃烧室的空气入口温度和气化室的蒸汽入口温度都有利于气化反应的进行。流化床共气化模拟中生物质与煤的掺混比例对温度场的影响如图7所示,随着生物质掺混比例增大,燃烧区的温度也随之降低。finite-rate/EDM模型结合了湍流以及动力学因素,提高了其模拟的准确性和可靠性,但该模型只适用于单步反应或双步反应,适用性仍有一定的限制,但可以与EDM模型形成互补,从而使涡耗散模型可以在更多条件下进行应用。
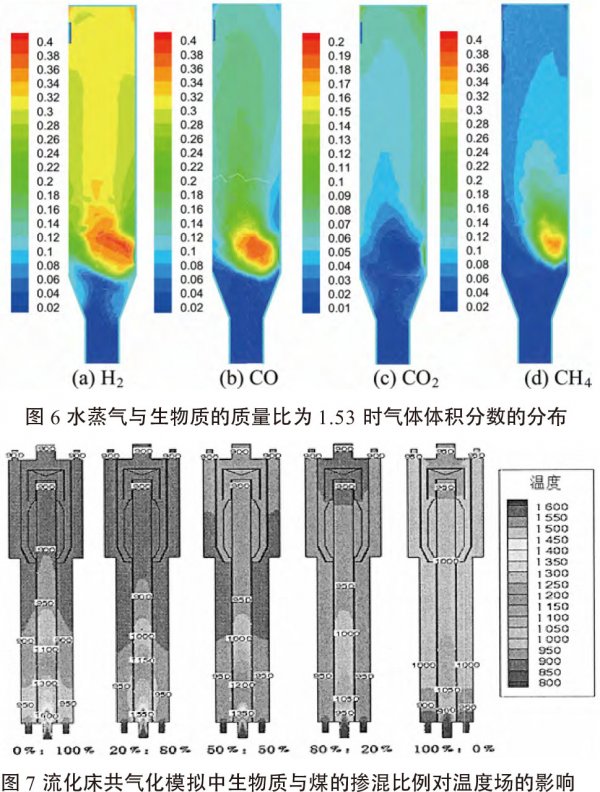
3.3.4其它模型
除了上述三种主要的耦合模型外,有研究人员还采用涡耗散概念模型(eddy dissipation concept,EDC),虽然其计算精度最高且反应机理也很详细,但由于计算量很大,故使用并不广泛。此外还有Flamelet模型以及PDF组分输运模型(compositon PDF transport)均可用于湍流气相反应的模拟。Flamelet模型适用于模拟快速反应,并且其不需要大量的网格以及较大的时间步长,故其模拟结果是相对粗糙的。而PDF组分输运模型对反应流的控制较EDC模型更加严格,由于考虑条件更加充分故计算量也更大,所以应用较少。
4结语
煤和生物质共气化是一种基于燃料单独气化技术发展起来的气化技术,由于在煤与生物之间存在着协同作用,故共气化可以弥补燃料单独气化的缺陷,如转换率低、产气热值低和焦油含量高等,同时还可提高能量的利用效率,减少化石能源的消耗。鉴于共气化实验的高温危险性、耗费时间长以及实验成本大等特点,基于CFD的数值模拟越来越受到研究人员的重视和青睐,并且为气化设备和流程的设计以及机理的探究都提供了很大的便利条件。目前,对于气化模拟中最为重要的湍流-气相反应耦合模型,主要有概率密度函数模型(PDF)、涡破裂模型(EBU)和涡耗散模型(EDM)这三大类,以及一些应用较少的其它模型。三类主要模型在各自应用范围内均有较好的表现,而综合考虑计算量、准确性和适用性,自EDM模型修正而来的有限速率/涡耗散模型(finite-rate/EDM)模型在共气化方面得到了广泛的应用。随着越来越多的气化模拟模型的开发,煤与生物质共气化的数值模拟也将会更加贴近真实的反应过程,为共气化研究提供更加经济高效的途径。
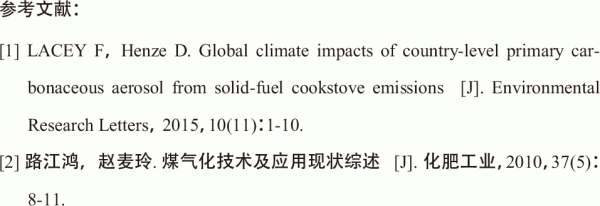
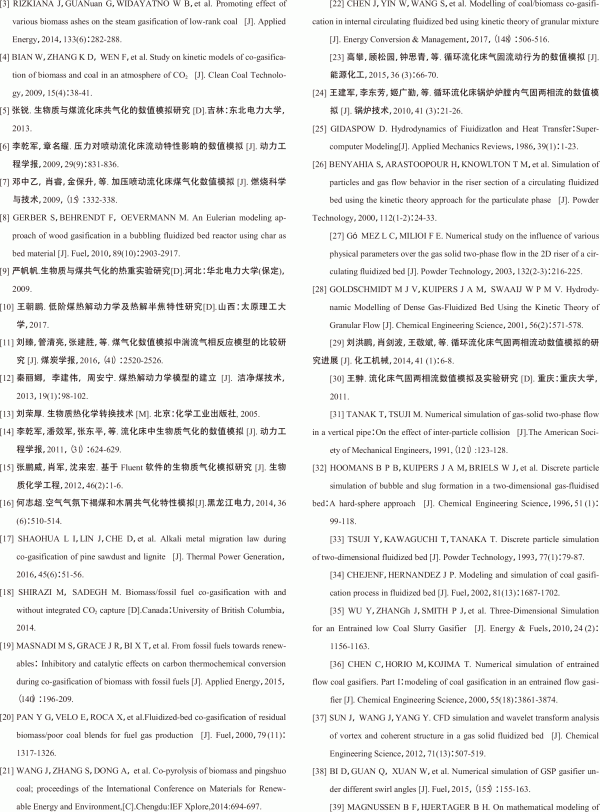
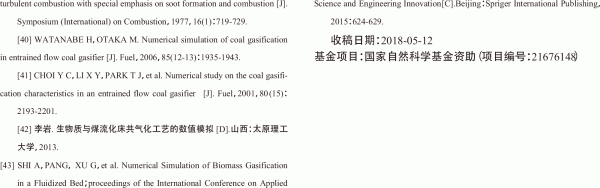 |