合肥市王小郢污水厂设计总规模为30×104m3/d,分一、二期建设,一期采用转刷曝气氧化沟工艺,二期采用转碟曝气氧化沟工艺,出水部分回用于城市景观用水,其余部分排入南淝河并最终汇入巢湖。提标改造工程实施后,王小郢污水厂主要出水水质目标为TN≤5mg/L、TP≤0.3mg/L、COD≤30mg/L、NH3-N≤1.5mg/L,均按年平均进行考核。
1工程改造设计情况
根据出水水质要求,改造工程的设计思路为二级处理阶段实现氨氮及COD的最终降解,同时最大限度地实现总氮和总磷的去除;深度处理部分实现截留SS、进一步脱氮除磷的出水把关作用。
1.1生物池改造设计
提标改造工程以二级生化处理强化脱氮除磷为目的,将原氧化沟工艺改造成以A2/O工艺为特征的工艺流程。将现况氧化沟划分出功能区独立的缺氧区和好氧区,利用原有氧化沟停留时间较长的优势,在满足硝化反应的基础上,为反硝化过程提供更大的池容,以强化反硝化过程。同时,在好氧区与缺氧区之间设置了好氧/缺氧可调节段,可根据操作环境和进水水质变化进行功能区的调整,使系统具有更强的稳定性和更大的操作灵活性。
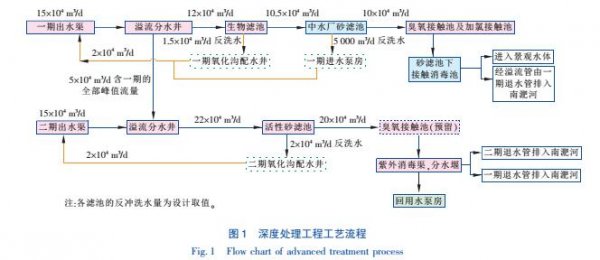
在好氧池末端设置后置反硝化区,其作用为降低进入回流污泥中的溶解氧、为缺氧池提供更好的运行环境,以及提供内源后置反硝化的反应条件。
对二级生物处理系统的改造和优化是提标改造工程的重中之重,直接决定改造工程的效果和成败。
1.2深度处理工程设计
结合氧化池改造及运行出水预测,对比出水目标分析深度处理部分的功能需求,确定本工程深度处理采用反硝化过滤+脱色和消毒的工艺流程,具体见图1,主要单体的设计参数见表1。
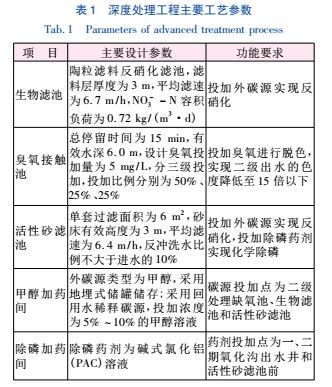
工程设计采用现场中试验证了反硝化滤池的工艺参数和适用条件,结合现场条件,最终通过工程招标确定深度处理的流程,即深度处理分为两路系统,一路为10×104m3/d一期工程二级出水进入生物滤池,出水经过现况V型滤池过滤、臭氧脱色和次氯酸钠消毒后,部分用于城市景观河道补水,超出需求部分排放南淝河;另外一期其余部分出水通过溢流井会同全部二期出水,进入活性砂滤池,出水经过紫外消毒后排放南淝河;部分出水用作厂区回用水,用于绿化、脱水机冲洗、臭氧循环冷却以及加药稀释用水等。
根据深度处理工程实施后新增污泥量的情况,对脱水机房进行扩建以及设备更新,同时增设污泥料仓。
2调试运行情况
2.1活性砂滤池
活性砂滤池调试工作在3月初开始,调试期间进水温度为13.8~21.8℃,进水量由10×104m3/d逐渐提高到设计规模20×104m3/d。根据调试进展情况,每天取样1~2次,按照国家标准方法进行分析化验。开始投加反硝化碳源后,基本在1周左右完成挂膜并产生明显的反硝化效果。调试期间,活性砂滤池进出水中总氮、氨氮、COD和总磷的变化情况见表2。
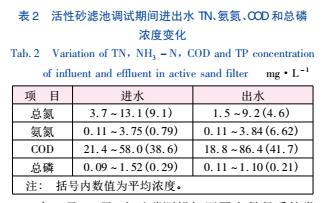
在4月12日,由于碳源投加回用水稀释系统发生故障,导致活性砂滤池中断运行10h;而系统重新启动后,滤池反硝化现象消失,滤池出水溶解氧为5~6mg/L。分析认为可能是由两方面因素造成的:
①活性砂滤池中断运行可能导致砂砾载体上生物膜发生脱落;②4月10日开始试探性投加除磷药剂,可能投加过量,导致活性砂滤池进水总磷浓度过低,进而对具有反硝化功能的生物膜的生长造成影响。在随后运行过程中,停止化学除磷加药,加大反冲洗水量,系统反硝化性能在一周左右恢复并稳定。由于后续污水厂二级出水总磷浓度一直很低,故后续调试没有继续投加除磷药剂。
活性砂滤池投加碳源可以实现一定的反硝化功能,调试期间总氮的平均削减浓度为4.5mg/L,出水硝酸盐平均浓度为2.1mg/L,调试初期出水中通常会有最高约2mg/L的亚硝酸盐,随着系统的运行,亚硝酸盐出水平均浓度通常降至1mg/L以下且相对稳定,本次调试过程中亚硝酸盐出水浓度范围为0.07~1.98mg/L。
通过投加除磷药剂实现同步脱氮除磷,除磷药剂投量需逐步小幅增加,避免对脱氮过程造成影响;同时滤池反冲洗废水量会增加。结合本次调试中出现的反硝化功能消失的情况,反硝化砂滤池前投加化学除磷药剂需谨慎,仅可以作为出水总磷的保障措施;主要的化学除磷应在二沉池前投药完成。
此外,在较大规模活性砂滤池系统工程设计过程中,应注意以下问题:①不同系列之间的配水均匀性;②活性砂滤池系统通过压缩空气气提作用促进砂层循环运动的特征,会导致滤池充氧、反硝化过程中外碳源消耗量的增加,从而增大运行成本;③反冲洗废水量是通过每套活性砂滤池系统的废水出水堰高度来调整,可控性差,人员操作维护量大;④单元数较多,操作检修繁琐。如果占地允许,将反冲洗废水进行泥水分离、浓缩减量后再排入二级处理系统中,将有效降低反冲洗废水对二级处理系统的水力复核和处理效果的影响。
2.2生物滤池
调试期间进水温度为15.4~21.4℃,进水量由3.5×104m3/d逐渐提高到设计规模10×104m3/d。
每天取样1~2次,按照国家标准方法进行分析化验。投加反硝化碳源后,约3~4天完成挂膜。调试期间,滤池进出水总氮、氨氮、COD和总磷的变化见表3。其中4月11日—13日,生物滤池出水总氮快速升至10mg/L左右,主要原因是碳源投加系统稀释水故障引起外碳源投加中断所致。恢复投加碳源后,出水总氮迅速降低并逐渐稳定在5mg/L左右。
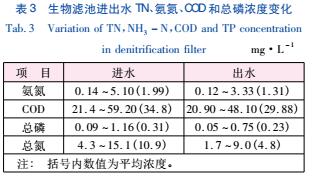
生物滤池系统设计滤速较快,运行相对稳定,适合较大规模污水处理厂。由于需要根据过滤过程中滤床阻力的变化进行定期反冲洗,需要配套反冲洗水泵、反冲洗风机等设备,以及配套建设反冲洗清水池和反冲洗废水池,系统配置较复杂;反冲洗期间,滤池不能过滤出水,因此在滤池格数较少时,需要考虑反冲洗期间,其他滤池的强制滤速不宜超过规范要求。生物滤池采用类似于V型滤池的长柄滤头进行布水布气,为了防止滤头堵塞、减少运行维护的工作量,需要做好滤池进水的预处理。本工程生物滤池进水提升后总进水渠设置了2mm的网板细格栅,同时在每格滤池的分进水渠设置1.2mm细格栅。
2.3投资与运行成本分析
深度处理部分投资情况如下:生物滤池(规模10×104m3/d)工程费为2600万元,臭氧投加系统(规模10×104m3/d)为1000万元,活性砂滤池(规模20×104m3/d)为4000万元。其中,滤池运行费用仅含提升、过滤及反冲洗废水排除的费用,不含反冲洗废水的处理;不含药剂费;工程投资为单体构筑物的工程直接费用。
3分析与讨论
二级处理效果是污水厂提标改造工程能否实现高标准出水的根本和基础。反硝化滤池作为二级出水水质把关,通过投加外碳源可以实现一定的总氮去除,但是需要特别注意控制滤池进水中的溶解氧浓度,以防破坏反硝化环境,并消耗外碳源。
为了解决噪音问题,在二沉池出水堰设置了降噪盖板(见图2),对跌水充氧进行了有效控制,进入出水槽内的溶解氧可由3~4mg/L降低到2mg/L以下。同时,检测还发现活性砂进水管路沿程不同的跌水位置同样也会导致水中溶解氧的增加,在进入活性砂滤池前的溶解氧达到6mg/L。运行过程中,在滤池总进水渠向分进水渠配水处通过闸门控制跌水高度,可有效降低跌水充氧,调整后将滤池进水溶解氧控制在3mg/L左右。此外,二沉池增加盖板后,可以有效降低沉淀池池壁附着藻类的滋生,降低对深度处理滤池的影响。
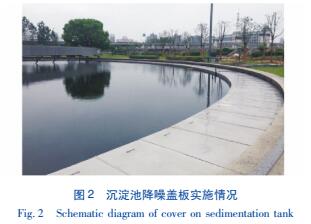
反硝化滤池会产生一定量的反冲洗废水及污泥,并增加滤池反冲洗的频率,这会增大系统运行的成本。在本工程中,由于占地的限制,反冲洗废水没有单独处理,而是排入二沉池前,频繁反冲洗会增大二沉池的水力负荷,增加运行能耗。
在不断提高的处理标准面前,确定设计出水标准时,考虑增加必要的前提条件,如考虑水中不可生物降解的COD和氮组分的浓度,避免针对一般性出水指标的处理,采用不符合我国现阶段国情、投资和运行成本均很高的工艺。本工程在设计过程中,对于COD<30mg/L的出水指标,制定了“进水不可生物降解的COD不大于20mg/L”的前提条件,当进水不可生物降解的COD>20mg/L时,利用高锰酸盐指数<10mg/L来考核。通过前期对本工程二级出水中总氮的组分分析,难于生物降解的有机氮浓度通常小于2mg/L。
4结语
以反硝化滤池为核心的深度处理工艺投资和运行成本均较高,而污水二级处理过程中的提标挖潜是实现高标准出水的根本。建议从制度上调动运行单位的积极性,例如上海、合肥等地正在推行的对高标准出水的奖励机制,可以实现很好的实际效果,值得推广和借鉴。
在我国目前的国情条件下,针对排放水体的水环境容量,因地制宜地确定污水厂出水标准应是我国污水处理行业发展的方向。而全面提高城镇污水收集率,实现已建成污水厂的正常运行,提高建设水平和运营管理,相对于一味提高污水厂的出水标准更有实际意义。 |